Updated: October 10, 2024
Master Data Management (MDM) is the modern solution for overcoming manufacturing’s data fragmentation while giving you the business insights and agility to act on them.
MDM combines the data governance and data quality necessary to understand operations for timely responses to shifting conditions.
But what exactly do you need your MDM to do?
These hubs should address two sets of requirements: business and technical ones. Solutions should be easy, accurate and scalable to fulfill business requirements.
They must be multidomain, cloud-ready, and capable of diverse implementation styles to fulfill technical requirements.
Not every MDM platform offers these capabilities.
However, the best deliver these advantages with accountability and customer assistance to beat data sprawl in manufacturing for good.
The Role of Master Data in Manufacturing
Master data plays a pivotal role in the manufacturing industry by ensuring consistency, accuracy, and reliability across all critical data domains—such as product, supplier and customer data.
With proper master data management (MDM) in place, manufacturers can avoid costly errors like production delays, stock inaccuracies and inefficient supply chains.
An MDM solution for manufacturing integrates these data points across disparate systems, providing a single source of truth that enhances decision-making. As manufacturing processes grow more complex, the role of master data management manufacturing solutions becomes even more crucial in driving innovation, efficiency and growth.
Business Requirements
Speed of implementation is critical to your MDM success. Competitive options in this space can be up and running in less than 90 days.
Your MDM should also be fast once it’s set up, and not complicated to use.
Affordable hubs enable you to start small and grow as needed.
Implicit to this requirement is the flexibility to find some initial success first and then grow when required without steep upfront costs. Scalability requirements are measured two ways: horizontally and vertically.
Hubs should scale horizontally to include increasing numbers of sources, yet scale vertically to handle large amounts of data. This requirement is critical for multi- domain deployments, since realistically you’ll only achieve limited value with single-domain offerings.
Common Master Data Management Use Cases in Manufacturing
The World Economic Forum reported in 2024 that only 39% of manufacturing leaders have successfully scaled data-driven use cases beyond individual product lines. This highlights the critical importance of mastering data and analytics across the enterprise to unlock full value from investments in data ecosystems and tools like Master Data Management (MDM).
From optimizing order fulfillment to improving supplier relationships, MDM ensures accurate, consistent data across systems, enabling manufacturers to drive efficiency and reduce costs. Below is an overview of common MDM use cases in the manufacturing industry and the business benefits they offer.
MDM Use Case in Manufacturing | Manufacturing Use Case Description | Business Benefits of MDM Use Case |
---|---|---|
Accurate, Rapid Order Fulfillment | Manufacturers face significant challenges in ensuring order accuracy and timely fulfillment due to fragmented systems and inconsistent data. MDM helps centralize and standardize data, ensuring order accuracy. | Improve customer satisfaction through fewer order errors, faster fulfillment, and enhanced visibility across the supply chain. |
Optimize Supplier Spend | Managing supplier data effectively is crucial to reducing procurement costs and improving supplier relationships. MDM unifies supplier data across systems for a comprehensive view of spend and performance. | Gain visibility into supplier performance, reduce procurement costs, and negotiate better contracts with accurate data. |
Accelerate and De-risk ERP Consolidation | ERP consolidation in manufacturing is often complex and risky. MDM ensures accurate, clean data is migrated to new ERP systems, reducing risks of data loss or inconsistencies during the consolidation process. | Reduce the risk of ERP implementation failure, accelerate consolidation timelines, and ensure data accuracy post-implementation. |
Reducing Indirect MRO Spend | Manufacturers struggle with managing Maintenance, Repair, and Operations (MRO) spend due to poor data quality and fragmented processes. MDM standardizes MRO data, enabling better control and cost management. | Reduce unnecessary MRO inventory costs, streamline operations, and improve procurement processes with clean, unified data. |
Manufacturers today also see the potential of smart factory solutions and generative AI to substantially impact their businesses. According to Deloitte’s 2024 outlook, 86% of surveyed manufacturing executives believe that smart factory solutions will be the key drivers of competitiveness in the next five years. These solutions, which rely heavily on trusted, high-quality data, underscore the importance of robust MDM systems to help manufacturers stay ahead in a competitive environment.
Can master data management reduce manufacturing costs?
Yes, master data management (MDM) can significantly reduce manufacturing costs by streamlining operations and minimizing waste. Inaccurate or incomplete data often leads to production errors, inventory overstocking and miscommunication between departments.
By centralizing and standardizing data, an MDM manufacturing solution ensures that all teams—whether on the factory floor or in procurement—are working with the same accurate information. This not only improves forecasting and inventory management but also optimizes supply chain operations.
Additionally, master data management manufacturing systems can automate routine tasks, reducing manual intervention and minimizing costly errors. In the long run, these efficiencies translate into tangible cost savings and better profit margins for manufacturers.
Technical Requirements
The most important technical requirement is your MDM solution should be multidomain. Single-domain options escalate costs each time a domain is added—which is almost inevitable in manufacturing. Multidomain options are flexible enough to handle everything from customer to supply chains concerns to avoid this problem.
You’ll need to cross-reference domains to get real-world value from your hub, like analyzing product and customer data for R&D efforts to bring desired features or products to market.
You should also consider what sort of cloud approach the platform uses. Reputable ones involve Platform-as-a-Service and Software-as-a-Service with cloud-native approaches like containers.
PaaS MDM gives you several tools (a relational database, MDM application, an unstructured data repository and more) to support distributed deployments with modern cloud architecture. It’s the right way to bring MDM to the cloud; putting a platform architected for on-premises into a VM and shoving it in the cloud is the wrong way.
Competitive MDM options support a range of implementation styles. Gartner defines four styles of implementing MDM: consolidation, coexistence, centralized, and registry. The consolidation style takes pointers to data in source systems and uses them without first cleaning up the source systems.
This approach really only works well for analytics, like running machine learning on customer data to improve customer experiences. The coexistence style is based on bringing together data in MDM, where it’s corrected before being updated in sources. Since MDM is synchronized with sources, this is good for decentralized or edge use cases.
The centralized style pulls data from sources into MDM, which becomes the only place where it’s updated before being pushed back to sources. This approach is beneficial for rapidly changing transaction data, like certain supply chain metrics or customer interactions. You’ll want the registry style for remote data and integrations between applications. It offers autonomy for sources in distributed settings. Top MDM hubs support all of these styles, which you’ll need depending on the use case.
Centralizing Data in Manufacturing
Centralizing data in manufacturing is essential for maintaining operational efficiency, especially as businesses scale and diversify their product lines.
With siloed data, manufacturers face challenges in decision-making, product traceability, and compliance. A centralized master data management solution helps break down these silos, enabling seamless access to real-time data across departments.
Whether it’s tracking raw material availability or monitoring product quality, centralizing master data manufacturing processes ensures consistent and reliable insights. Moreover, centralization enhances collaboration between teams, improves regulatory compliance and allows for more accurate reporting, which is critical in today’s fast-paced manufacturing landscape.
Vendor Selection
There are three main considerations for vendor selection. Obviously, you’ll want a product that fulfills the business and technical requirements. You should also ensure your vendor is accountable and remains a part of your team, even after your purchase. Finally, you should do an RFI to help you with the selection process.
This step should trigger the ongoing assistance your vendor provides, which is important for maximizing the value from your MDM. Vendors like Profisee excel in each of these areas to consistently support you throughout your MDM journey.
Picking a Winner
MDM solves the manufacturing pain point of being overwhelmed with data spread out across ERPs, sources and locations. Still, if it doesn’t meet the aforementioned technical and business requirements, it won’t be easy to use in this vertical. It must be fast, affordable, and scalable to uphold the business, while also being multidomain, cloud (native) ready, and supportive of multiple implementation styles.
How to implement an MDM solution in the manufacturing industry
Implementing an MDM solution in the manufacturing industry involves a strategic approach tailored to the unique challenges manufacturers face, such as managing vast amounts of product data, responding to supply chain disruptions, and compliance requirements.
The first step is conducting a comprehensive data audit to identify inconsistencies and gaps in existing data. Once this is complete, manufacturers should select a master data management manufacturing solution that aligns with their specific needs. This could involve integrating with existing ERP systems, ensuring the solution supports real-time data synchronization, and enabling cross-departmental collaboration.
Establishing data governance policies and clearly defining roles ensures the solution’s success. With a robust MDM manufacturing strategy, businesses can achieve faster product launches, reduce operational inefficiencies and increase overall agility.
In Summary: Building Your Own Vendor Selection Criteria
You’ll find plenty of options that support one or two of these requisites. Profisee is one of the rare vendors to support all of them—including the vendor selection criteria. Profisee’s MDM rectifies silos to provide comprehensive visibility into your manufacturing data for agile business action. It’s just what the industry needs.
Interested in learning more? Download ‘The Complete Guide to Master Data Management for Manufacturing’ below.
Source System | Example Systems and Function | Master Data Examples |
---|---|---|
CRM Systems | Systems like Salesforce, HubSpot and Pipedrive capture vital customer interactions and relationship data, like deals closed and pipeline sources | Name, primary address and date of birth |
ERP Systems | Systems like SAP, Dynamics 365 and NetSuite record information about customers such as their names, billing and shipping addresses, payment methods and purchase history | Company name, billing address and tax ID |
Marketing Automation Platforms | Marketing automation tools like Marketo and Pardot record valuable information on customer engagement and preferences, but they can also capture customer information through lead forms | Name, email address and segmentation data (e.g., customer, partner, prospect) |
Ecommerce and POS Systems | Ecommerce tools like Shopify or Salesforce Commerce Cloud and point of sale (POS) tools like Square or NCR can also capture customer information | Name, primary address and loyalty program data |
Social Media Platforms | Social media platforms like TikTok and LinkedIn can provide valuable demographic and psychographic data about your audience, but determining which of this data is master data is not as black-and-white as it is with other systems. Certain demographic information (such as college-educated) about customers might be considered master data, but it ultimately boils down to what specifically your organization decides to label master data | Profile ID and certain demographic data like age, race and education |
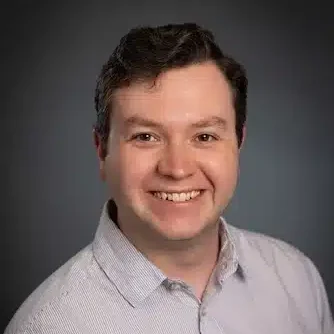
Forrest Brown
Forrest Brown is the Content Marketing Manager at Profisee and has been writing about B2B tech for eight years, spanning software categories like project management, enterprise resource planning (ERP) and now master data management (MDM). When he's not at work, Forrest enjoys playing music, writing and exploring the Atlanta food scene.