Table of Contents
Did you know there are 7,500 different kinds of apples? Did you also know that people make an average of 35,000 choices during any given day?
Even at this very moment, you chose to click and read this blog. We are constantly making choices — both big and small — and in today’s world, the possibilities are seemingly endless.
The same principle not only applies to your enterprise manufacturing data, it gets compounded as manufacturers grow by acquisition, consolidate ERP systems or uncover new sources of enterprise data. When it comes to finding the right approach to managing/consolidating fragmented data, you have an important choice.
The Choice Theory states that personal choices fall into five basic human needs: survival, love/belonging, power, freedom and fun. Making a decision that furthers one’s interests is not a surprising concept. But how does it relate when you are solving an internal business problem for a group as opposed to a personal one?
Managing Manufacturing Data at Scale
Like many industries, manufacturing is full of choices. What is the best way to produce a product at scale? How do we stay within budget but still produce a quality product? From the machines creating the products to decision-making employees making lasting decisions, choices are everywhere.
The problem is that manufacturers have a complex and potentially intimidating data problem that is throwing a wrench in making trusted decisions. Much like choices in general, manufacturing data is everywhere.
Typically, organizations start by supporting manufacturing operations at a single location. Manufacturing organizations typically achieve this by implementing data tools like ERPs, procurement systems or different databases at each location.
But issues surface as manufacturing organizations begin to scale. Data complexity increases with the introduction of each new product line, geographic region and acquisition.
Manufacturers may have initially wanted decentralized enterprise data so leaders at each location could quickly make their own decisions that best support their operations. But today, many manufacturers want to leverage their scale and require access to more centralized data, even if their operations remain decentralized.
Approaches to Managing Manufacturing Data
The remaining question is: What can manufacturing companies do about their data challenges and what choices do they have to fix their data silo or ERP sprawl?
In the spirit of the Choice Theory, we sat down and thought about the five basic human needs that drive the decision-making process. When approaching these needs, it’s important to ask the following questions:
- What could give your company the power and freedom to make trusted decisions across the company?
- How can you help employees connect their goals to the broader company mission once everyone has access to the same, high-quality data?
- What could make your job more fun by having trusted data?
- What could help your company survive in any fiscal environment?
- Most importantly, what could help YOUR company grow and thrive in any fiscal environment?
When it comes to leveraging your manufacturing data and overcoming a fragmented data landscape, there are three common approaches to resolving the issue:
1. Manually Cleaning Manufacturing Data
Many organizations initially try and solve this issue by doing everything themselves. They hand-stitch their data together spanning across multiple tools, data types, IT systems and use cases.
They also often hire more employees as they grow and/or acquire additional companies – creating even more spreadsheets. It becomes increasingly tedious and difficult as the process must be repeated when the data changes.
Not only is it needlessly repetitious, but it becomes increasingly difficult to keep up as data volumes grow and systems grow in complexity.
2. Consolidating ERPs for Manufacturing Data
At first, this consolidation process would appear to be an easy fix to the problem at hand. It eliminates the data sprawl issue while hitting your data fragmentation at its core.
Unfortunately, this is far too costly and time-consuming. As a result, the process can take years to accomplish. With consolidating your many ERPs comes the roadblock of individual units serving their purpose. No business enjoys wasting time and money when there is an effective alternative.
3. Master Data Management for Manufacturing
Easily the most viable option of the three, master data management (MDM) is faster and more efficient. Its automation trumps any of the cons of the manual approach while improving data quality through initiated data governance and record-matching across your multiple systems.
Inevitably, manual data entry will occasionally lead to missing values or invalid data. With MDM, a single manual correction is stored into the platform and applied for all future cases — helping you save time, money and effort in maintaining your critical manufacturing data.
Interested in learning more? Download ‘The Complete Guide to Master Data Management for Manufacturing’ below.
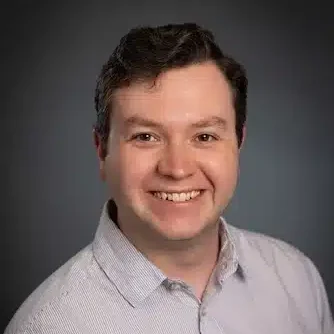
Forrest Brown
Forrest Brown is the Content Marketing Manager at Profisee and has been writing about B2B tech for eight years, spanning software categories like project management, enterprise resource planning (ERP) and now master data management (MDM). When he's not at work, Forrest enjoys playing music, writing and exploring the Atlanta food scene.